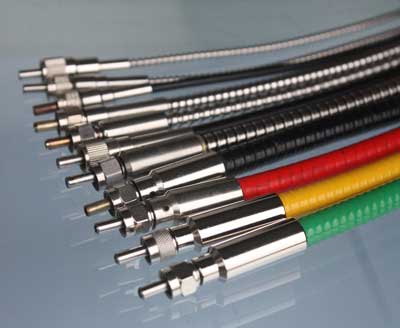
During the last three decades, the advancement and adoption of both solid-state laser and fiber laser systems have increased dramatically. They are particularly important in the industrial, medical, scientific, military/defense, semiconductor capital equipment sectors.
The days of delivering laser beams through free space optics or cumbersome, bulky, and expensive articulating arms have long passed. The modern era requires efficient, durable, reliable, and flexible fiber optic delivery systems. Fiber optics can precisely deliver powerful beams at high efficiencies to the target, be it a medical laser performing a surgical procedure or an industrial laser performing manufacturing tasks.
High Power Requires High Purity
Due to the high power handling requirement of these laser delivery systems, large multimode step index optical fibers are commonly used. These fibers have very high-purity synthetic fused silica cores and fluorine-doped silica cladding which can handle tremendous amounts of energy without failure.
In general, these fibers can handle 1.3KW*2mm of energy density in continuous wave (CW) mode, measured at 1,064nm wavelength, which is what a neodymium-doped yttrium aluminum garnet (Nd:YAG) laser operates at. The larger the fiber core, the more photons and energy can be delivered through it. Typically, fibers from 200 to 2,000 microns in diameter are used for laser delivery applications. Borosilicate and plastic (PMMA) fibers have substantially lower power density capabilities than fused silica fibers. Therefore, they cannot be considered for high power laser delivery applications.
In addition to selecting the right size fiber, the best suited connector design must also be chosen for the application. Higher energy and power mean more heat will be generated at the connector end. This heat must be managed and handled properly, otherwise the connectors and probe will fail.
Connector Types and Benefits
Laser application fiber optic assemblies are available with two primary varieties of connectors.
SMA-905 Connectors
SMA-905 connectors come in two types, standard and drilled out. Standard SMA-905s are combined with high temperature epoxy while FSMA (air gap) connectors feature ferrules with drilled openings. These openings help to provide 360 degrees of air flow around the fiber itself, and between the cladding and the ferrule. This air gap is important in that it eliminates the need for epoxy at the fiber face, which heats during use, helping to cool the entire connector body.
Then there are the copper drilled-ferrule SMA-905s. These connections function in the same way as other drilled-ferrule connectors, but with the added heat transfer properties of copper.
D-80 Connectors
D-80 connectors offer superior performance over other connectors, including power and heat handling capability. We offer two D-80 styles, one copper ferrule and one copper ferrule plus additional sapphire ring at the base. The sapphire ring serves to better center the fiber inside the connector, and also protects the ferrule from energy accumulation and return.
Assembly Polishing
Finally, polishing the ends of fiber optic assemblies for laser applications is extremely crucial. Typically, they are fine flat polished to 0.3-micron specifications. After polishing they are cleaned many times to ensure the fiber probes are completely free of contaminants. These polishing and cleaning procedures can be done manually, or with either automated polishing or CO2 laser polishing equipment.
Speaking of cleaning, these fused silica fiber optic assemblies, which can deliver up to 650 watts of laser power, must be cleaned regularly. We recommend cleaning their ends with isopropyl alcohol and an optical cloth, such as Kimtech, both before and after use. For ferrule-drilled connectors, applying compressed air to force debris from inside the airgap is also recommended.
Power Handling Capabilities of Silica-Silica Assemblies
Connector Type | 100 Microns | 200 Microns | 400 Microns | 600 Microns | 800 Microns | 1,000 Microns | 1,500 Microns | 2,000 Microns | |
---|---|---|---|---|---|---|---|---|---|
Standard SMA-905 | ![]() | 40 Watts | 50 Watts | 175 Watts | 225 Watts | 250 Watts | 275 Watts | X | X |
Drilled-Out SMA-905 | ![]() | X | X | 300 Watts | 350 Watts | 350 Watts | 375 Watts | 400 Watts | 400 Watts |
Copper Ferrule Drilled-Out SMA-905 | ![]() | X | X | 350 Watts | 600 Watts | 600 Watts | 600 Watts | 600 Watts | 600 Watts |
Copper Ferrule D-80 | ![]() | X | X | 400 Watts | 650 Watts | 650 Watts | 650 Watts | 650 Watts | 650 Watts |