If you’ve been in manufacturing for a while, you might remember a time when quality was somewhat of an afterthought, secondary to considerations like price, expediency, and availability. Gradually — and understandably — product quality has become a major concern and with it rose the popularity of quality management systems.
More recently, evolutions in process-related thinking are starting to move beyond “simple” process management and consider other factors such as risk. This is where Process Risk Analysis comes into play.
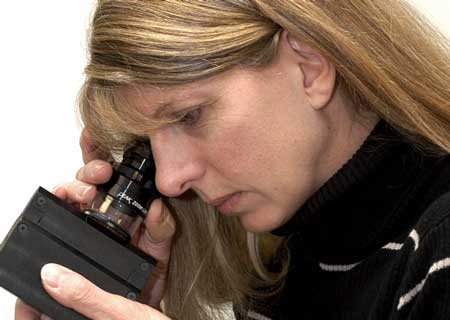
Process risk analysis involves calculating risks, developing plans to minimize uncertainties, then act to mitigate the associated risks, and see plans through. This is done in part by gathering and analyzing data from a process and using it to develop consistent decision making. In this way, you can ensure that you can consistently and reliably manage risk in order to maintain a quality standard. A process risk analysis plan, by design, includes the quality assurance processes and documentation. Process risk analysis is meant to be an all-encompassing method of analyzing and communicating as much detail about any given process as possible; it aims to involve all team members for the most universal understanding of process flow, and its associated risks and controls.
The result of a properly conducted process risk analysis is a control plan for each process. This includes the continual performance of quality check protocols, that will help maintain a consistent quality level in your products. AT FTI, we implement unique Risk Analysis protocols for each work cell. They are not one size fits all, and must be scaled and adapted to the huge variability in product, production processes, material, and other factors.
Assessing the risk of a any process can be broken up into four key considerations. First is: what in this process could/might fail in some way? For every potential issue that that question unveils, there are two three follow up questions: IF the failure does occur, how sever are the consequences to the product/customer? How often does this occur?; and How do we control the process that may cause this failure?
This simple line of questioning is the foundation for establishing production practices that minimize risk for you and helps ensure output at a consistent and higher level of quality.
Stay tuned for our next blog, where we will talk about why you should care about process risk analysis.